What is Pendulum mill?
The mining pendulum grinding mill, also known as the suspended roller mill or Raymond mill, is a type of grinding equipment that combines “ring-roller” grinding with air flow screening and pneumatic conveying. It is widely used in the grinding process of minerals such as calcite, limestone, talc, gypsum, barite, and gypsum, with a fineness of up to 400 mesh.
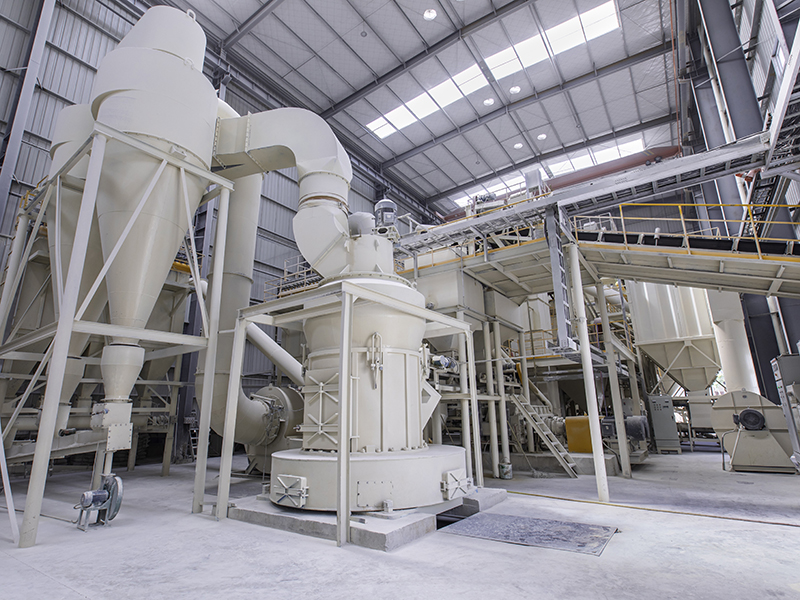
custom sites
325 mesh calcite powder plant
capacity 8-10 TPH
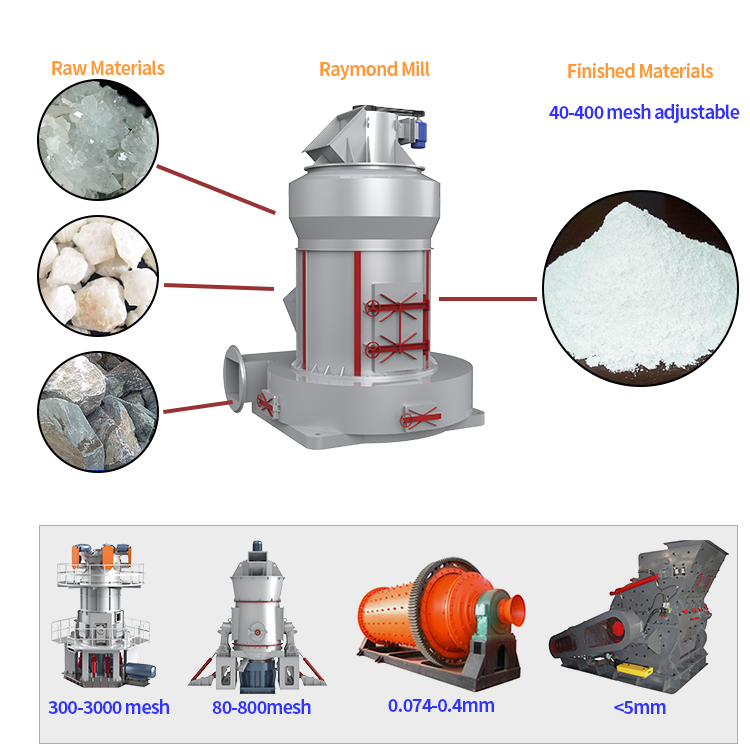
What is the difference between pendulum mill and Raymond mill?
Pendulum mill and Raymond grinding machines are often confused in the industry. Even some materials refer to the two as different names of the same equipment. However, there are differences in technical iteration, structural design, performance parameters, etc. The following provides a detailed comparison from the aspects of core definitions, structural details, performance characteristics, and applicable scenarios:
Raymond Grinding Machine: Originating from the Raymond Company in the United States in the late 19th century, it is one of the earliest “ring-roller” type grinding machines. It belongs to traditional grinding equipment, with relatively outdated technology and relatively fixed structure and performance.
Pendulum mill grinding machine: It is a new type of equipment that has been upgraded and improved based on the Raymond mill. By optimizing the structure, improving the grinding method and the classification system, it has achieved higher efficiency and wider applicability. It belongs to the “upgraded version” or “improved type” of the Raymond mill.
The main differences between the pendulum mill and the Raymond grinding machine lie in the following aspects:
Component | Raymond Mill | Pendulum Mill |
---|---|---|
Grinding rolls and grinding rings | The number of grinding rollers is relatively small (usually 3-4), and the roller diameter is also small. The grinding pressure mainly relies on centrifugal force, and the pressure is relatively weak. | The number of grinding rollers is greater (4-6), the roller diameter is larger, and some models have an additional hydraulic device to assist in pressurization, resulting in stronger grinding pressure. |
classfier | Using the traditional impeller classifier, the classification accuracy is relatively low, and the range of finished particle size is narrow (mainly 80-325 mesh). | Equipped with upgraded turbine classification machines (such as large-blade conical turbines), some models also incorporate variable frequency speed regulation, resulting in higher classification accuracy and a wider particle size range (80-400 mesh, with some reaching 600 mesh). |
Base structure | Most of them have detachable bases, which cause significant vibration. If used for a long time, they are prone to causing components to loosen or crack. | It adopts a frame-type integral base, which has strong earthquake resistance, reduces vibration during equipment operation, and prolongs the service life of components. |
Sealing system | The traditional sealing method is prone to dust leakage and has poor environmental performance. | By adopting gas sealing or multiple sealing technologies, the positive pressure part of the main unit is fully sealed, resulting in minimal dust leakage and meeting environmental protection standards. |
Transmission system | Single motor drive, fixed speed, grinding efficiency is limited. | Some models are equipped with dual motors or variable frequency speed control, allowing the rotational speed to be adjusted according to the hardness of the materials, making them more adaptable. |
From the above data charts, it can be seen that the Raymond mill and the pendulum mill are the same product. They are used in the same way, but there are slight differences in their structures. Customers choose to use the pendulum mill or the traditional Raymond mill based on the characteristics of the materials they process.