Recently, our company’s aluminum ash pendulum Raymond mill is under intense installation in Zhengzhou, Henan Province. It is known that this customer processes aluminum ash powder with an aluminum content of about 10%. After being ground by the pendulum Raymond mill, the aluminum slag is removed. The product is mainly used for the treatment of solid waste, and the required output is 5 tons per hour.
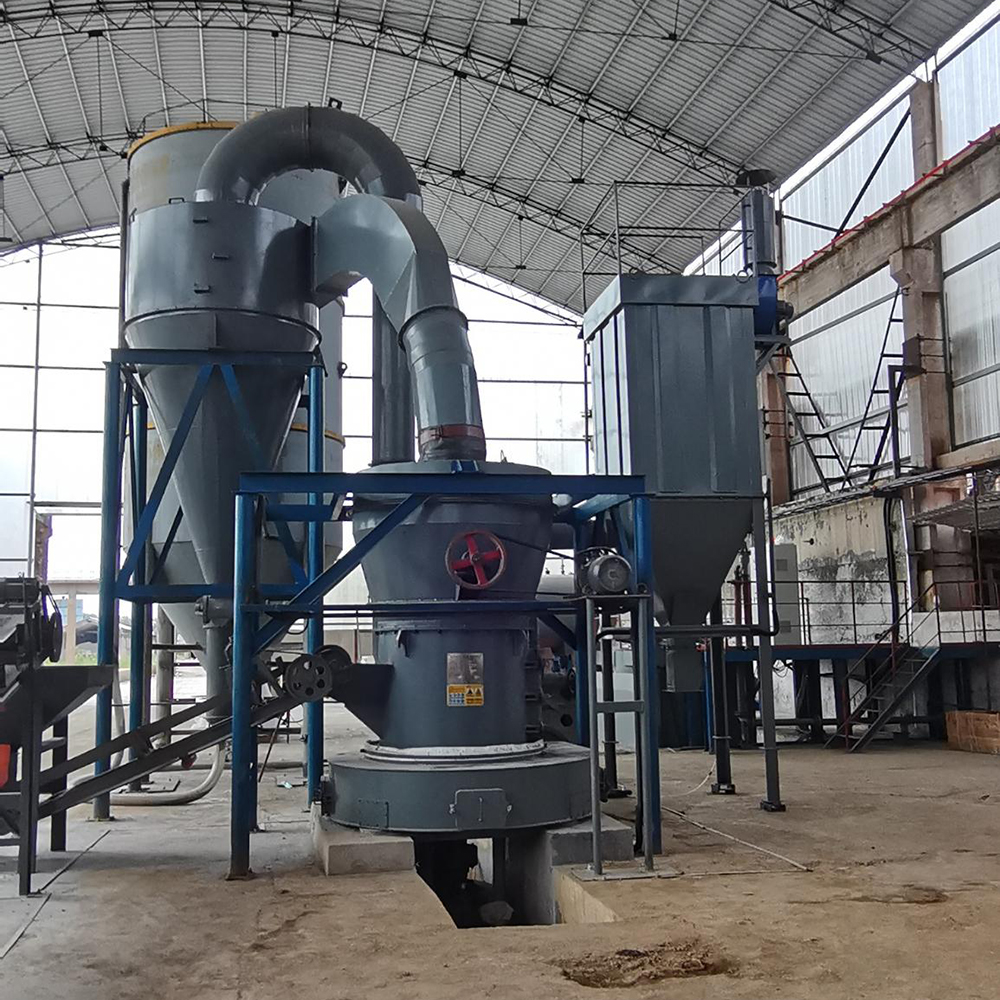
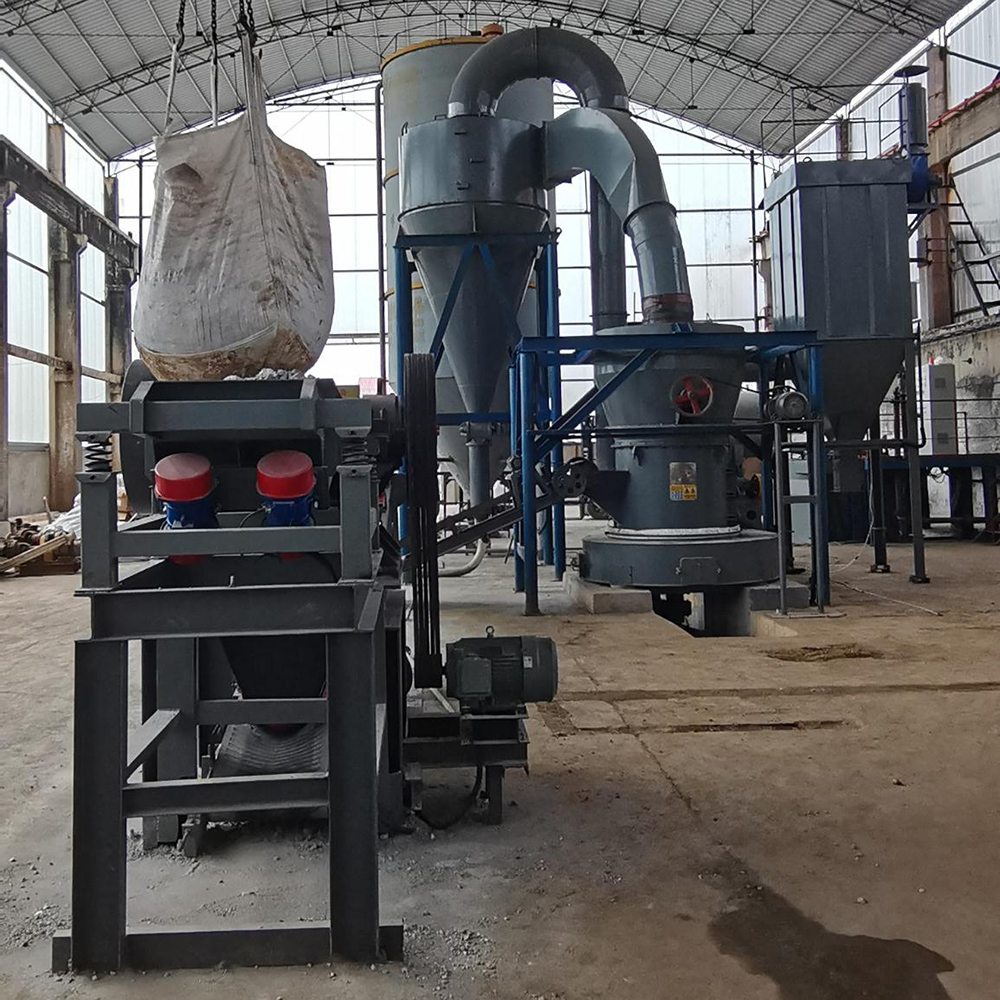
The processing of aluminum slag has always been a challenging issue in the grinding field. This is mainly because aluminum slag contains metallic aluminum and some other metals. During the grinding process, these metal impurities cause severe wear on the equipment. Many domestic manufacturers of pendulum Raymond mills have no good solutions for processing aluminum slag. Our company has conducted in-depth research on aluminum slag and has collaborated with domestic universities and research institutes. After five years of dedicated research, we have made multiple technical improvements to the pendulum grinding mill, making our pendulum Raymond mill an ideal equipment for processing aluminum slag.
At present, our company’s aluminum slag pendulum grinding mill has been certified by customers in many places across the country. The products are distributed in over ten regions including Henan, Shandong, Hebei, Hubei, Hunan, Sichuan, Xinjiang, Guangdong, and Guangxi. The total installed capacity of this equipment has reached 50 units. These devices are currently operating well and have been highly recognized by customers.
Why is it so difficult to grind aluminum slag into powder?
The difficulty in grinding aluminum dross stems from the combination of its complex composition, physicochemical properties, and specific issues arising during the grinding process. A detailed analysis is as follows:
I. Complex Composition: Mixed Hard/Soft and Tough/B brittle Components with Vastly Different Grinding Behaviors
Aluminum dross, a by-product of aluminum smelting and processing, has a complex and variable composition, mainly containing three key substances whose properties directly increase grinding difficulty:
- Metallic aluminum (elemental Al): It has extremely high toughness (elongation up to over 40%) and is a typical “hard-to-crush” material. During grinding, metallic aluminum particles are not easily broken by mechanical forces; instead, they may undergo plastic deformation due to extrusion and friction, forming flake or fibrous particles that wrap around the rotor and screen of the grinding equipment, causing blockages and a sharp drop in efficiency.
- Aluminum oxide (Al₂O₃): It has extremely high hardness (Mohs hardness 9, second only to diamond) and strong chemical stability. During grinding, aluminum oxide particles cause severe wear to equipment components such as grinding discs, rollers, and steel balls, significantly shortening equipment life. Meanwhile, due to its high hardness, a greater grinding force is required for crushing, leading to a substantial increase in energy consumption.
- Aluminum nitride (AlN) and impurities: Aluminum nitride typically accounts for 5%-20%. It itself has high hardness (Mohs hardness 7-8) and easily reacts with moisture in the air (AlN + 3H₂O → Al(OH)₃ + NH₃↑). The generated aluminum hydroxide colloid may bond particles, causing “agglomeration” during grinding. Additionally, aluminum dross often contains salt impurities such as sodium chloride and potassium chloride, which are highly hygroscopic. During grinding, they tend to absorb moisture and form lumps, further hindering particle refinement.
II. Particle Morphology and Structure: Irregularity and Susceptibility to “Protective Agglomeration”
The original particle morphology of aluminum dross is highly irregular, including blocky, acicular, and flaky structures formed by cooling of molten materials, as well as inclusions of metallic aluminum and oxides (e.g., aluminum particles wrapped in an aluminum oxide film). This structure leads to:
- Uneven force distribution during grinding, making it difficult to achieve uniform crushing. Some particles may not be effectively ground due to “force dead zones”;
- The ductility of metallic aluminum causes particles to undergo “plastic deformation” rather than “brittle fracture” during crushing. Instead, they may “wrap” surrounding oxide particles, forming “protective agglomeration” and further increasing the difficulty of refinement.
III. Chemical and Safety Risks in Grinding: Exacerbating Equipment Wear and Process Complexity
- Adhesion and Corrosion Caused by Chemical Reactions: As mentioned earlier, the aluminum hydroxide colloid generated by the hydrolysis of aluminum nitride and the deliquescent substances from hygroscopic salts adhere to the inner walls of grinding equipment and grinding media (e.g., steel balls). This not only reduces grinding efficiency but may also corrode equipment (especially electrochemical corrosion of metals by salts).
- Safety Hazards Limiting Grinding Intensity: Metallic aluminum in aluminum dross is flammable. Intense friction during grinding can generate high temperatures (local temperatures up to 300°C or higher), potentially causing aluminum powder to self-ignite. Meanwhile, if the concentration of grinding dust reaches a certain level, there is a risk of explosion. Therefore, the grinding process requires strict control of rotation speed and temperature (e.g., adding cooling systems), which sacrifices part of the grinding intensity and indirectly increases the difficulty of grinding.
The core difficulty in aluminum dross grinding lies in the “compositional contradiction”: the coexistence of the toughness of metallic aluminum and the hardness of aluminum oxide, combined with the adhesion and corrosion caused by chemically active substances (aluminum nitride, salts), and the restrictions on processes due to safety risks. These factors make it difficult for ordinary grinding equipment and processes to handle aluminum dross efficiently. Addressing this issue typically requires targeted optimizations, such as adopting a “crushing-grinding” 分级 process, using special wear-resistant and anti-adhesive grinding materials, and incorporating inert gas protection or low-temperature cooling systems.